FLIR Optical Gas Imaging and Thermal Imaging Solutions Help Uncover Invisible Risks at Petrochemical Plants
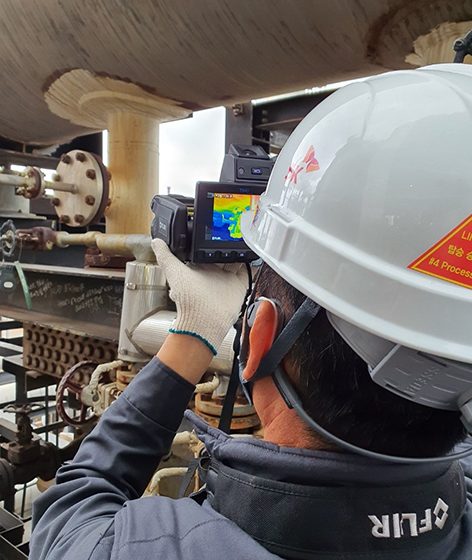
K Energy, Korea’s leading oil refining corporation, uses FLIR optical gas imaging (OGI) and thermal imaging cameras for safety inspections at the Ulsan CLX plant, one of its key refineries.
To the Ulsan CLX inspection team, this FLIR technology is critical to maintaining safety throughout the plant. Given the massive scale of the Ulsan CLX plant, its inspection team uses an impressive array of inspection equipment for a wide range of purposes: from portable thermal imaging cameras, such as the FLIR Exx-Series and T-Series, to FLIR GF320 and GF346 OGI cameras. In particular, the FLIR GF320 has become an integral part of the inspection process, and the Ulsan CLX plant has added more than ten cameras to its arsenal of inspection equipment.
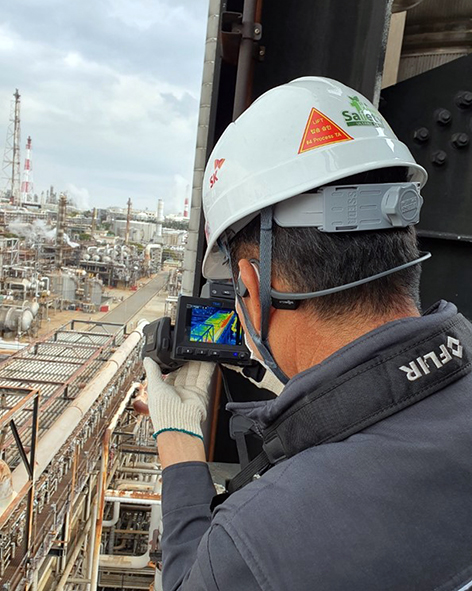
The Ulsan Complex, or “Ulsan CLX”, is an indispensable facility for SK Energy that develops and produces most of the company’s petrochemical raw materials and finished products. It also develops and refines crude oil, and produces petrochemical products, films, yarns, and textiles. Ulsan CLX has a crude oil refining capacity of 840,000 barrels per day, making it the largest of its kind in Korea and the third-largest in the world for a single petrochemical plant.
SK Energy’s Core Facility
SK Energy is making every effort to ensure the safety of its massive Ulsan CLX plant while also avoiding unnecessary downtime by implementing fastidious safety management protocols, preventive inspections, and regular maintenance activities. The company employs a variety of safety strategies, including daily safety measures, minor maintenance works done every year, and major maintenance projects every three to four years.
During regular maintenance, SK Energy deactivates parts of its production line and disassembles equipment for detailed inspections and repairs. It also checks old equipment and replaces catalyst materials. With more than 46,000 kilometers of piping and equipment spread across 21 production processes, it is impossible to inspect the entire complex with regular inspections. As such, SK Energy inspects the production processes at Ulsan CLX on a rotating basis, surveying eight to nine production processes at a time. These regularinspections alone require hundreds of thousands of technicians and personnel for months. Regular maintenance is key to managing the safety of facilities and catching potential faults before they cause a system to break down. This is not to say regular maintenance can completely eliminate equipment failure or safety incidents. For example, at any given regular maintenance session, tens of thousands of components are disassembled and reassembled, valves are closed and opened when old parts are replaced with new parts. Since everything is done by hand, there is a small possibility that workers fail to secure a screw or valve, which can potentially lead to abnormal heating or gas leaks.
Why Refineries and Petrochemical Facilities Need FLIR
When pipes at an oil refinery or chemical plant leak, the escaping gas can be toxic. These toxic gases can sometimes have no discernible smell or color, which is why precautions must be taken to ensure worker safety.
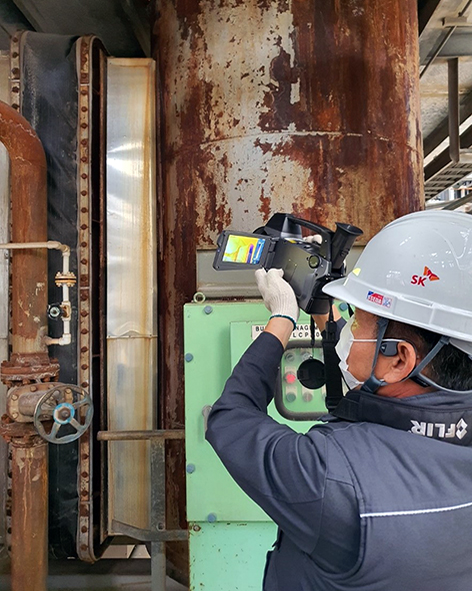
Equipment safety and management are also extremely important. Refineries and chemical plants have numerous pipelines interconnected horizontally and vertically. These pipes are often covered with insulation and refractories to protect the plant from extreme temperatures. However, when used for a long time, gaps may appear between the insulation and pipes, resulting in heat loss. Failure to identify and address these problems early can lead to a costly shutdown of the entire facility. As Deputy Senior Manager for the Ulsan CLX inspection team, Bo-lim Lee, explains, “FLIR’s optical gas imaging cameras and thermal imaging cameras ensure the safety of our workers from harmful gases that cannot be seen with the naked eye. They protect the entire facility and helps to protect the complex from hidden dangers.” While the inspection team deploys a range of FLIR products, their most highly-rated device in terms of usability and reliability is the GF320. Introduced first at the Ulsan CLX in 2012, this gas-finding camera is used to scan the entire facility for hydrocarbon or VOC leaks in valve connections after major maintenance projects. Lee says using the GF320 to scan the entire facility after maintenance is considered virtually mandatory at the Ulsan CLX.
Deploying the FLIR GF320
Previously, the Ulsan CLX used a gas detector to detect harmful gases. While products such as “sniffers” (toxic vapor analyzers) can detect the presence or absence of harmful gases leaked into the air, they are not capable of identifying the specific location where the gas was leaked. Sniffers also require the user to physically approach the inspection site, greatly increasing safety concerns. On the other hand, the GF320 can visualize harmful gas leaks and identify the leaked location. Inspectors can sweep the camera across a 2/3 target area from a distance—improving safety—and avoid any gas clouds when moving in for a closer look.
Other bennefits provided by the GF320 include thermal imaging, stability against changes in the surrounding environment, durability, and ease of use. Thanks to its utility and reliability, the GF320 is a popular piece of equipment not only at Ulsan CLX’s Inspection Team, but also at its production departments, which have purchased more than ten additional GF320 cameras. Lee says, “We strongly recommend the GF320 to other oil refineries and chemical plants.”
FLIR Technology Ensures Operator Safety and Facility Maintenance
In addition to the GF320, SK Energy uses the FLIR GF346 OGI camera as well as the FLIR T640 and E60 thermal cameras and FLIR GF309 furnace camera to ensure the safety of its facilities.
The FLIR GF309 is filtered to a special wavelength so that it can penetrate flames for inspections inside boilers and heaters. Using a GF309, SK Energy recently discovered deterioration caused by coking while inspecting a heater tube at one of its affiliates. Inspectors monitored its equipment around the clock using the GF309 camera, analyzing which components displayed temperature fluctuations. They quickly identified the defective heater tube and were able to remove and clean it without having to shut down the facility. The Ulsan CLX inspection team employs a FLIR GF346 OGI camera to detect leaks from its two carbon
monoxide boilers. Normally, SK Energy converts the toxic carbon monoxide gas into non-toxic carbon dioxide before discharging it into the air. But since both boilers are old, they tend to leak carbon monoxide from their weldings. The GF346 allows the inspection team to pinpoint the source of leaks and repair them before the carbon monoxide can cause any safety issues. As for the FLIR T640 and E60, these thermal imaging cameras are portable and convenient enough to be widely used for daily safety inspections. In particular, the T640 and E60 can easily detect heat loss on horizontal and vertical piping that have gaps in the insulation. “FLIR’s cameras are excellent in visualizing invisible risk factors during facility safety inspections because of the easy-to-read thermal images they provide,” says Lee. He adds, “We expect FLIR’s range of optical gas imaging and thermal imaging cameras to play an important role in our safety inspections and worker protection.
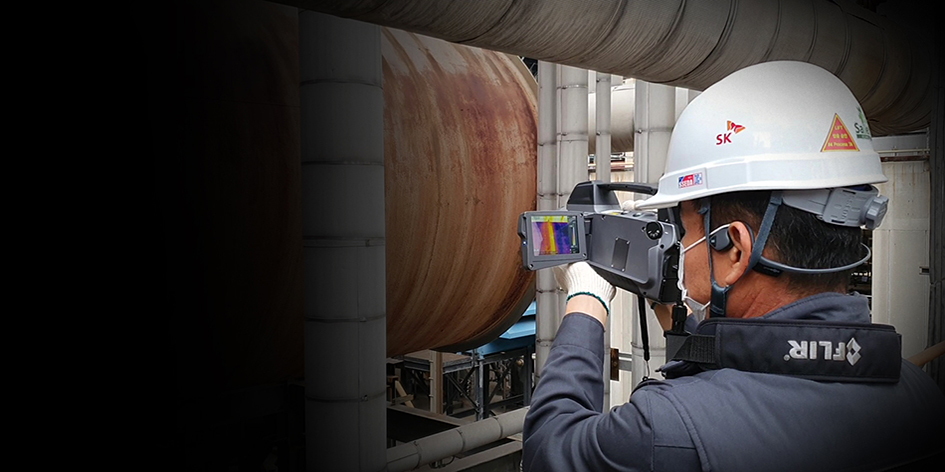